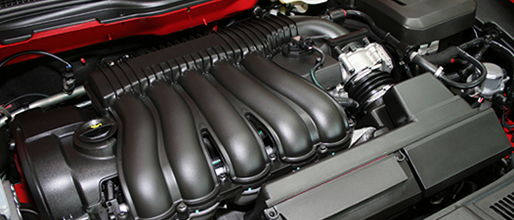
Optimized combustion: increasing the efficiency of diesel engines and of the overall unit
As well as developing alternative drives, the automotive industry is relying on further improving and increasing the efficiency of traditional combustion engines. This concerns firstly fuel injection for diesel engines, but also the efficiency of the overall unit.
Efficient diesel engines
The proportion of vehicles with diesel engines in Germany is just 50%, with a similar percentage applying for Europe. The main argument in favor of diesel engineering is common knowledge – the fuel consumption is lower compared to petrol engines. To further reduce consumption and thus also emission output, it is essential to have high-precision pressure measurement.
Fuel injection in diesel engines
In diesel engines, the very high pressure of the fuel injection system atomizes the fuel very finely. Finer atomization at higher pressures greatly improves the speed of the combustion process, and at the same time reduces emissions, because the particles are smaller in size. In the first series of cars with diesel fuel injection, the Fiat Croma TD i.d., which appeared for the first time in 1988, the pressure was just 1000 bar. Now the pressures achieved rangefrom 2000 to 2500 bar, and the level is still rising.
Common rail fuel injection
Pressure transducers from HBM are used, for example, in developing common rail fuel injection, which is also called “accumulator fuel injection”, as the pressure generation is totally separate from the actual fuel injection process. With this technology, a high-pressure pump constantly keeps the fuel at a high pressure level. The timing and volume of fuel injection are controlled by the electronics.
P3TCP pressure transducer series
The high-precision pressure transducers of the P3TCP series are used on the test benches of the automotive industry to optimize common rail fuel injection.
The “top class” models have a working accuracy of between 0.1 and 0.2 % (depending on the measuring range) and are available for pressures from 0 to 3,000 bar. This puts them exactly in the working range of today’s fuel injection systems and connected high-pressure pumps. The high accuracy guarantees that the measurement results can be reliably reproduced. An integrated (PT100) temperature measurement ensures temperature compensation.
But the P3TCP series is also geared up for a further increase in the pressure level. With the“BlueLine” models, maximum temperatures between 5,000 and 15,000 bar can be determined – and this is with an accuracy class of 0.25 at 5,000 bar.
Both the “Top Class” and “BlueLine” models allow precise control and therefore optimized diesel fuel injection settings.
Optimizing the overall unit
A topical and ever more important aim in the development of engines and transmissions is optimizing the energy efficiency of the overall unit. To do this, it is necessary to metrologically determine the energy consumption of all the components and auxiliary units involved.
Because a modern combustion engine does not just supply power to the transmission, but also to the generator or the air conditioning compressor, for example. This supply of power also has to be metrologically recorded, so that optimization can occur. Losses at the camshaft, cam belts or timing chains must also be recorded and optimized. This can be done with great accuracy by measuring the torque at the mechanical interfaces of the respective units, for example, at the crankshaft or at the camshaft.
Customized torque transducers
HBM provides specifically customized torque transducers for this task. These are installed between the belt or chain sprocket and the auxiliary unit. The resultant parasitic loads such as bending moments, radial and axial forces, are largely compensated by the transducer design.
Utilization on test benches and in road tests
The transducer has a compact, ultra-flat design, so that it can remain in position even when an entire engine is being installed in a vehicle This allows it to be used both on test benches and in road tests. Its operating temperature range is also suitable for the extreme values that occur in field tests (journeys in hot and cold climates). The data transmission and energy supply of the rotor are non-contact and wear-free, via a telemetry system. Data can be output directly to a measuring computer via digital or analog interfaces. The wide supply voltage range covers both cars and trucks.
Accuracy class 0.2%
The accuracy class of the torque transducers is typically 0.2%, with typical measuring ranges at 100 Nm. This allows accurate and high resolution measurements, according to requirements. The dimensions of the transducer, as well as the fixing dimensions, can be adjusted to meet customer requirements.