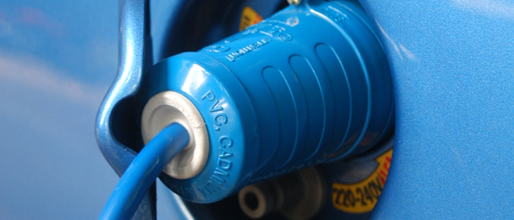
"现代轻巧的设计" - a fundamental basis of an energy efficient future
In August 2009, the German federal cabinet approved a national development plan for electro-mobility on which relevant technological development is to be based and which is to promote market introduction of plug-in hybrid and electric vehicles. To survive in the competitive internal markets, Germany will have to become the lead market for electro-mobility. In particular the storage performance of rechargeable batteries will require increased efforts to enable the German automotive industry to maintain and reinforce its global competitiveness. The German federal government's goal: One million electric vehiclesshall be driving on Germany's roads by 2020.
The Fraunhofer Gesellschaft has long been aware of the importance of this topic. In a joint project called "Fraunhofer Systemforschung Elektromobilität" (Fraunhofer electro-mobility system research), 33 Fraunhofer Institutes are cooperating to efficiently support the changetoward a sustainable "all-electric economy".
The term 'system research' captures the spirit of the program. It points out that coordinated development is required in all stages along the value chain of electro-mobility. This applies to energy generation, transport and distribution of energy through power networks, interfaces between power network and vehicle, energy storage through new vehicle designs using innovative infrastructure and concepts for usage and billing. Only through coordinated development of all relevant components will we be able to implement the vision of a society based on electro-mobility.
One of the research topics that are addressed is lightweight design. In a field of activities that is as innovative as electro-mobility, providing lightweight vehicle structures is a central challenge to ensuring sufficient cruising ranges.
New approaches of Structural Health Monitoring (SHM) spanning industries and applications play an important role in lightweight design. This method permanently integrates sensors into structures to enable continuous monitoring of their functional status. The SHM concept combines classical and innovative sensors with an automated analysis infrastructure.
In general, the safety of lightweight structures, for example in aviation, has been sufficiently ensured by manual inspection at specific intervals so far. Test engineers carry out tests on critical points using non-destructive test procedures. Between these inspections, it is possible that potential damage may not be detected and therefore must not exceed critical values during the time of use.
Reducing the number of inspections and increasing the intervals cuts maintenance and repair costs. However, this requires larger component thicknesses of the structure to prevent potential cracks from attaining a critical size between the inspections. In this context, reduced intervals would promote lightweight design, however, at the same time increase costs through more frequent manual inspections.
This dilemma can be resolved by carrying out automatic structural tests. Thus enabling both cost and weight to be reduced. Here, adequate sensors are used for recording and analyzing an overall picture of the status in short intervals.
HBM and Fraunhofer LBF have been cooperating in this promising field already for some time in order to find practicable approaches, because innovative sensors such as strain gages for structural integration and optical strain gages are particularly suited to be used, for example, with fiber compound structures. Vibration strength tests and corresponding analyses using innovative sensors have already been carried out in cooperation.
A wing mock-up fitted with 18 metal and 16 optical strain gages was shown at the Aerospace Testing Expo and the aviation show in Paris to illustrate potential fields of applications.
Based on sensor data and using durability methods, an assessment of the remaining service life of a structure that was loaded, damaged and repaired in its individual history must be allowed for in future. This evaluation of a structure's status is to enable maintenance and repair measures that can be planned more reliably and faster.
Monitoring the use of lightweight structures with integrated sensors and deriving decisions eventually depends directly on the availability and reliability of the test equipment. However, introducing this technology in batch production requires manufacturing processes to be adapted to enable smooth integration of test and measurement equipment into the fiber compound structure.
Structural Health Monitoring combined with new materials will be one of the future key technologies for implementing affordable and at the same time reliable lightweight design. All industries providing products for an energy-efficient future will benefit from this development.