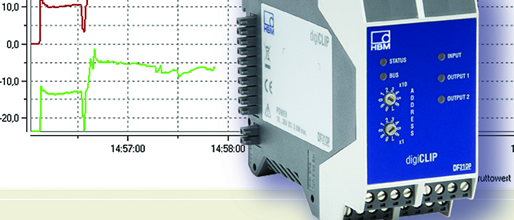
Central control of all the devices of a production system with Device Type Managers (DTM)
You do not need to be an expert to be able to install a printer for a PC without difficulty. Usually all that is required is to have the relevant driver installed to prepare the data for the print job, and then you can start printing.
Device Type Managers (DTM)
With Device Type Managers (DTM), this principle of operation can now also be used for the metrological monitoring of Production systems. As with printer drivers, the DTM covers all the functions required for the parameterization, operation and diagnosis of a field device, including a graphical user interface and a Help system.
Increasing the efficiency of Production systems
Integrating DTM pursues the following aims: reducing maintenance outlay and downtime, as well as improving product and production quality – the entire system can be optimized with DTM. On the one hand, demand-oriented maintenance of components is possible, so that routine maintenance activities are no longer required. On the other hand, system availability is increased, which achieves a clear increase in the efficiency of the Production systems.
Central data acquisition
To achieve these aims, data must be acquired from all the relevant parts of the system and be made available to the service engineers as easily and conveniently as possible – and this must be done at a central point of the system. Until now, the difficulty has been that the installed devices are usually heterogeneous - they come from different manufacturers, for example, and therefore also use different communication protocols. To diagnose the current status of a device, the relevant software always had to be installed, and its operation is also tied to the particular manufacturer, of course, so four devices from different manufacturers also means four different software solutions. This is exactly the problem that is solved with DTMs and the Field Device Tool (FDT) interface.
Integrating intelligent field devices into a single system
An FDT defines a unified interface that allows intelligent field devices (even from different manufacturers) to be integrated into a single system, if they have a relevant DTM at their disposal. Let us clarify this by going back to the example of a PC. For a word processing program to address a printer driver correctly, the interface between the application (the word processing program), the operating system and the driver, must be clearly defined. In an engineering system, this function is taken over by the FDT.
DTM – perfectly matched to the device
This unified interface makes it possible to integrate any devices into a system, whatever their manufacturer or fieldbus protocol. Only one relevant DTM has to be made available with the particular device. The DTM usually comes from the manufacturer and is thus perfectly matched to the device. The specific strengths and advantages of the device are retained, because it has optimum support. A particularly convenient feature is that as with PC printers, there are only marginal differences between the graphical user interfaces of all the DTMs, so that you do not first have to learn how to use it, even with a new device.
FDT frame application
Systems with an FDT interface are called FDT containers or FDT frame applications and contain the application itself – control system, monitoring, configuration, engineering or asset management. The defined FDT interface ensures interoperability. Or to put it another way, it guarantees problem-free operation of all DTMs in the required frame application.
The monitoring system example
The advantages of a system fitted with an FDT interface can easily be seen in the example of amonitoring system. Whereas previously, malfunctions had to be localized directly on the device itself, now all that is needed is to double-click the relevant DTM that has usually already sent out an alarm indication, and the service engineer is given a status report and can begin an extended diagnosis – and this can be done from a central point, from which all the parts of the system can be managed via the relevant DTM. As, for the most part, parameterization also takes place via DTM, immediate error recovery is often possible as well.
digiCLIP with DTM
HBM has developed a DTM specifically for digiCLIP industrial amplifiers, to fully exploit the aforementioned advantages. As digiCLIP also supports TEDS, the electronic data sheet in the transducer, parameterization, just like monitoring and maintenance, is child’s play. Because digiCLIP detects transducers fitted with TEDS totally automatically – there is no need for complicated settings. This is Plug & Measure in the truest sense of the words.
Do you already have a digiCLIP and now want to use DTM as well? Not a problem – HBM can provide you with the appropriate Device Type Manager as a free download.
The advantages of FDT/DTM technology
- Free choice of products without any system integration restrictions
- Central access to all field devices
- Ultra user-friendly
- Supports all fieldbus protocols
- DTM management
- Unified DTM user interface
- Full support of all device functions
- The system is less complex
- Your staff need less training
- Demand-oriented maintenance
- The reduction in downtime increases efficiency and reduces cost